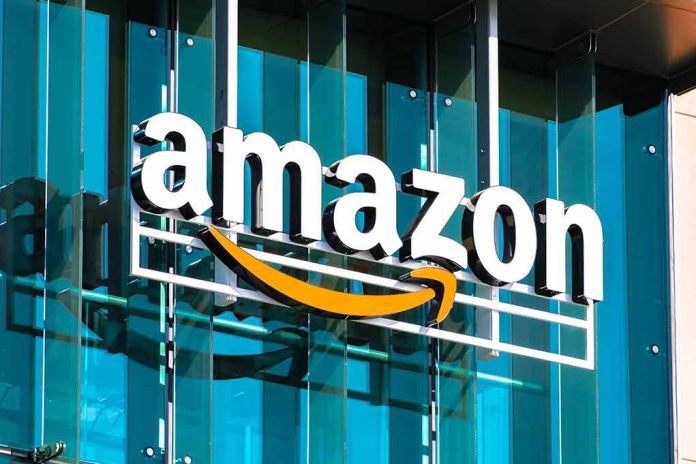
Amazon’s “Vulcan” robot is revolutionizing warehouse operations with human-like touch sensors that can handle 75% of inventory tasks, potentially transforming the jobs of hundreds of thousands of workers across the company’s global distribution network.
Key Takeaways
- Amazon’s Vulcan robot can pick, stow, and rearrange 75% of Amazon’s inventory items with a sophisticated sense-of-touch system
- Currently operational in Spokane, Washington and Hamburg, Germany with plans for wider deployment across the U.S. and Europe
- The robot achieves nearly human-comparable speeds, with test robots stowing at 224 units per hour compared to humans’ 243 units per hour
- Vulcan uses AI and force-feedback sensors to adjust its grip dynamically and can request human assistance when encountering unfamiliar items
- Amazon claims the technology creates new technical job categories rather than eliminating positions, with employees gaining skills through robotics apprenticeship programs
Advanced Tactile Technology Transforms Warehouse Operations
Amazon’s Vulcan warehouse robot represents a quantum leap in automation technology, featuring an articulated arm with a spatula-like paddle and a second arm equipped with a suction cup and AI vision system. What makes Vulcan truly revolutionary is its advanced force-feedback sensors that provide a sense of touch, allowing it to adjust its grip strength dynamically when handling various products. This technological breakthrough enables Vulcan to navigate complex warehouse environments with unprecedented precision and adaptability.
“Vulcan represents a fundamental leap forward in robotics. It’s not just seeing the world, it’s feeling it, enabling capabilities that were impossible for Amazon robots until now,” explains Aaron Parness, as stated by Daily Caller.
The robot’s AI software was trained on thousands of real-world touch scenarios to refine its grip and speed. When Vulcan encounters obstacles or unfamiliar products, it can learn from mistakes and alert human workers for assistance. This adaptive learning capability allows it to handle the vast majority of Amazon’s inventory while maintaining operational efficiency and product safety. Currently, Vulcan is operational in facilities in Spokane, Washington, and Hamburg, Germany, with plans for wider deployment across Amazon’s network.
If you haven’t toured an Amazon warehouse, I highly recommend it.
You might meet their new Vulcan robot with a sense of “touch.”
Here’s my takeaway from being inside the machine.
As you enter the ginormous warehouse, a giant American flag hangs from the ceiling, along with the… pic.twitter.com/Px7yc0BhwM
— Shannon Jean (@ShannonJean) May 9, 2025
Human-Robot Collaboration Rather Than Replacement
Despite concerns about job displacement, Amazon emphasizes that Vulcan is designed to work alongside human employees rather than replace them entirely. With over 800,000 U.S. workers, Amazon claims the introduction of robots creates new job categories and technical opportunities. The company offers a mechatronics and robotics apprenticeship program to help employees transition into more skilled technical roles as automation increases. This approach reflects Amazon’s strategy of using robots to handle physically demanding tasks while redirecting human talent to more complex work.
“Working alongside Vulcan, we can pick and stow with greater ease. It’s great to see how many of my coworkers have gained new job skills and taken on more technical roles, like I did, once they started working closely with the technology at our sites,” says Kari Freitas Hardy. Daily Caller
A recent Senate investigation highlighted increased injury rates during peak seasons at Amazon warehouses, suggesting that robots like Vulcan could potentially reduce these risks by handling physically strenuous tasks. While full automation remains unachievable for now, the robot-human collaboration model appears to be Amazon’s focus. The company directly addresses employment concerns by emphasizing continued hiring despite technological advances.
Performance Metrics and Technological Challenges
In addition to Vulcan, Amazon is testing specialized robots nicknamed “Stow” and “Pick” in its fulfillment centers. During testing, the Stow robot successfully moved items 85% of the time, with some failures resulting in product damage. The Pick robot demonstrated an even higher 91% success rate but rejected nearly 20% of pick requests due to vision failures or damage concerns. These metrics reveal both the promise and limitations of current warehouse robotics technology.
“Over March 2025, humans stowed at an average rate of 243 units per hour (UPH) while the robotic systems stowed at 224 UPH,” notes the paper. The Register
Amazon faces significant challenges in improving these systems, particularly with visuomotor policy learning (VMP) – the AI approach that allows robots to learn tasks through observation rather than explicit programming. As Amazon’s researchers acknowledge, “A key challenge of deploying learned VMPs is their lack of interpretability in failure cases.” To address this, the company plans to implement Real2Sim modules that create digital replicas of real-world scenes to model failures and improve performance through better training data.
With human stow rates potentially improving if robots handle the top rows of storage pods (eliminating ladder work), the synergy between human workers and robotic systems appears to be Amazon’s strategic direction. This collaborative approach aims to leverage the strengths of both humans and machines while addressing the physical limitations and injury risks associated with traditional warehouse work.